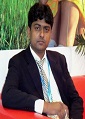
Rashid Mahmood
Surge Laboratories Private Limited, Pakistan.
Title: Cleaning Validation in Pharmaceuticals
Biography
Biography: Rashid Mahmood
Abstract
Cleaning Validation can be defined as “The process of providing documented evidence that the cleaning methods employed within a facility consistently controls potential carry-over of product (including intermediates and impurities), cleaning agents and extraneous material into subsequent product to a level which is below predetermined levelsâ€. The cleaning validation program shall primarily address the cross contamination of active ingredients of previous product into next product by means of sharing common equipment contact surfaces. In accordance with this, all equipments that have product contact surfaces shall be brought into the purview of cleaning validation. Special emphasis shall be given to cleaning procedure requirements as part of design requirement. Cleaning is one of the critical processes in pharmaceutical manufacturing. It is critical to avoid carryover of trace amounts of either active or other materials from one batch to another in order to avoid cross-contamination of the subsequent product. For that reason, equipment used in pharmaceutical manufacturing must be cleaned meticulously, and the cleaning procedure used must be validated. In the pharmaceutical industry, Good Manufacturing Practices (GMP) requires that the cleaning of drug manufacturing equipment be validated. Many different validation techniques can demonstrate that the manufacturing equipment is cleaned and essentially free from residual active drug substances and all cleaning agents. Common analytical techniques in the validation process include HPLC, Spectrophotometry (UV/Vis) and TOC. Cleaning validation must be performed using a pre-approved protocol. Selection of appropriate sampling to demonstrate that residues are removed to an acceptable level is vital for the success of cleaning validation. In addition, use of sampling techniques such as recovery study for swab and rinse and thorough visual inspection can reduce the number of samples required for cleaning validation. This article provides background on cleaning validation and the associated regulations, cleaning methods, validation strategy, and new product introduction. It also covers validation samples, acceptance criteria, clean hold time, training, change control, and revalidation. The intention of this article will be to define a comprehensive approach to the validation of cleaning procedures in pharmaceutical manufacturing facilities. It defines the basic concepts and terms associated with cleaning validation in the pharmaceutical industry. It also serves as a guide from which master plans, protocols and reports may be compiled